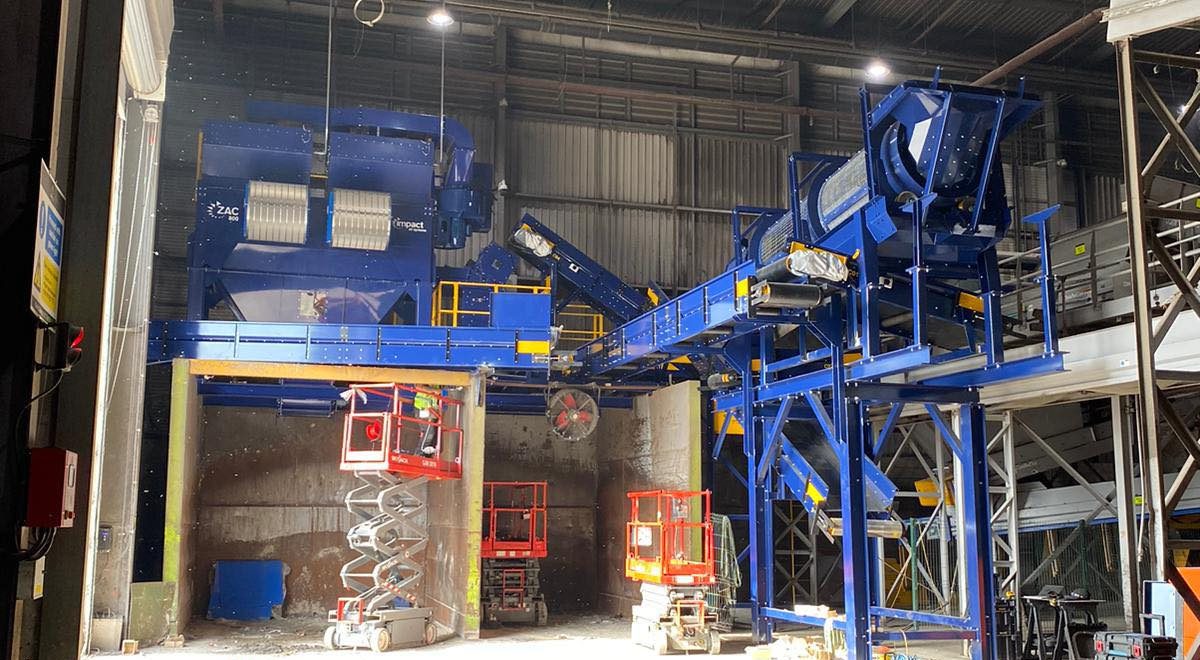
MRF Upgrades
22 Aug 2024
MRF Upgrade for CasePack
Take a look at the successful installation of a Material Recovery Facility (MRF) Retrofit by our team, in collaboration with Impact Air Systems. The integration of KME’s durable trommel and transfer conveyors with the innovative ZAC system from Impact Air has revolutionized Casepacks‘ co-mingled waste cleanup process. This system adeptly separates lightweight materials such as paper, film, dust, and plastic from heavier items like glass and metal, optimising the recycling stream and reducing contamination.
This project is a testament to the power of collaborative innovation and teamwork. By combining KME’s expertise in mechanical sorting with Impact Air’s proficiency in air-based separation, the two companies have created a process that enhances the overall efficiency and effectiveness. The ZAC system’s precision in segregating materials not only improves the quality of the recyclables but also minimises the environmental impact by reducing the amount of waste that ends up in landfills.
The success of this retrofit installation could serve as a blueprint for other facilities looking to upgrade their waste processing systems.
——————————————————————————————————————–
MRF Upgrade for Viridor
The successful upgrade of the viridor Avonmouth Material Recovery Facility (MRF) and the integration of new conveyors supplied by KME highlight their commitment to enhancing operational efficiency.
Their Energy Recovery Facility (ERF) plays a crucial role in environmental conservation by diverting significant amounts of non-recyclable waste from landfills, thus reducing pollution. It generates substantial amounts of electricity from this waste which supports the energy needs of tens of thousands of homes.
The plastics reprocessing facility further contributes to sustainability by transforming vast quantities of plastic into recycled materials, thereby feeding valuable resources back into the economy and reducing the reliance on virgin materials. These initiatives reflect a forward-thinking approach to resource management and energy production.
——————————————————————————————————————–
Why Choose KME for your MRF Upgrade?
Ken Mills Engineering Ltd (KME) has a long-standing reputation for excellence in the design & manufacture of MRF upgrades within the UK.
With a history of designing and installing sophisticated waste processing systems, KME’s expertise is also evident in other recent projects like the Neath Port Talbot MRF in South Wales. This facility features advanced metal separation technology, including a Permanent Overband Magnet and Eddy Current Separator, which are crucial for the efficient recovery of recyclable materials.
Our commitment to innovation and customer satisfaction has solidified our position as a leading provider in the industry. We welcome anyone to enquire about how we can help improve their MRF facilities.
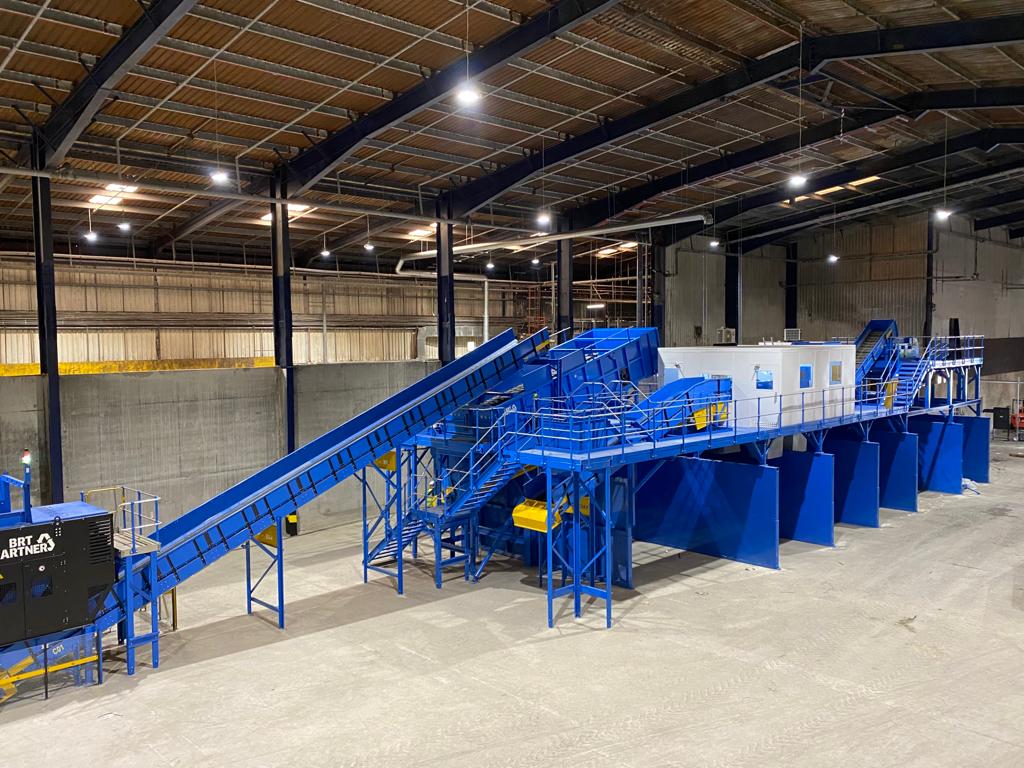