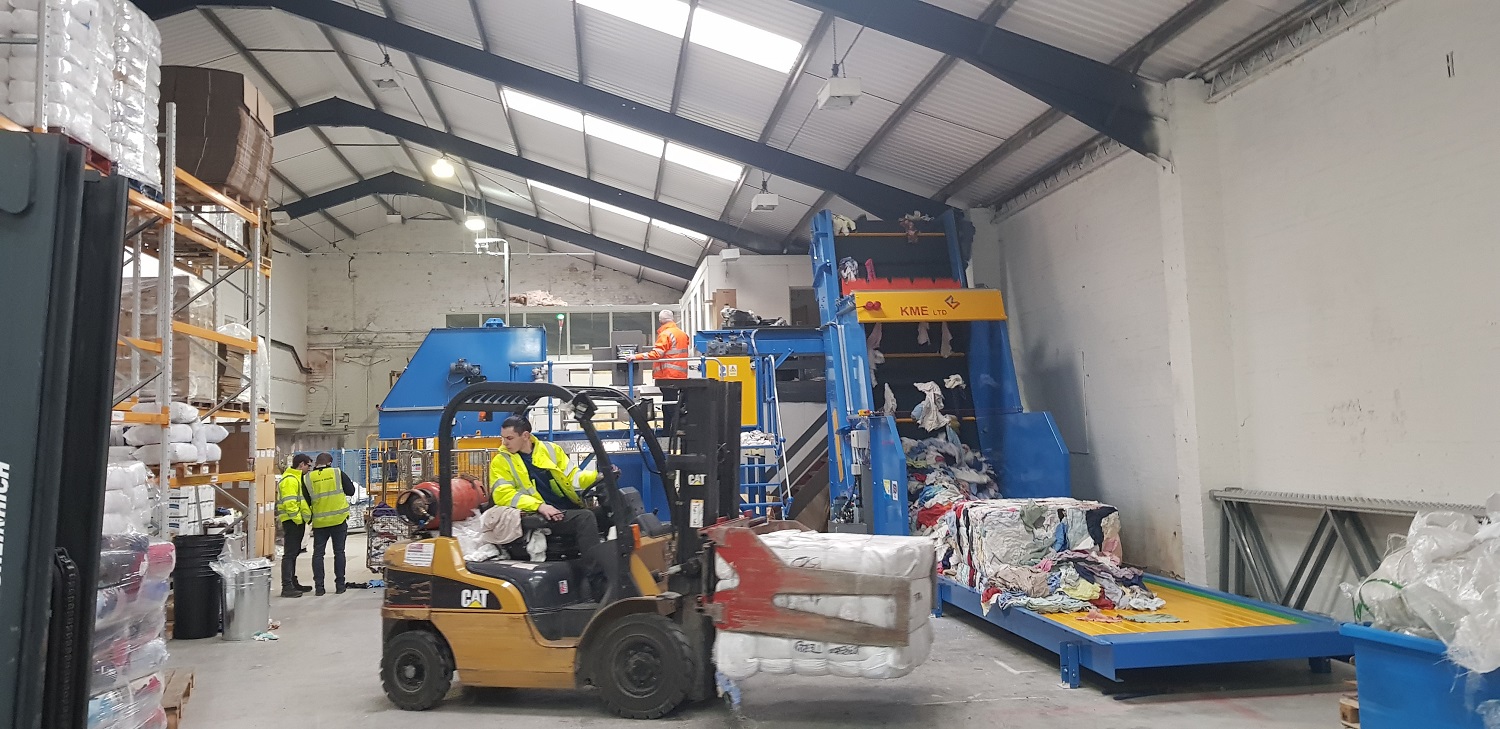
Wiping Rag Production
29 Oct 2024
Ken Mills Engineering (KME) has recently upgraded a textile processing line featuring a bale breaker with two K10 balers designed specifically for wiping rag production. This advanced setup brings substantial benefits to customers in the wiping rag industry, including increased production capacity, enhanced product quality, and reduced operational costs.
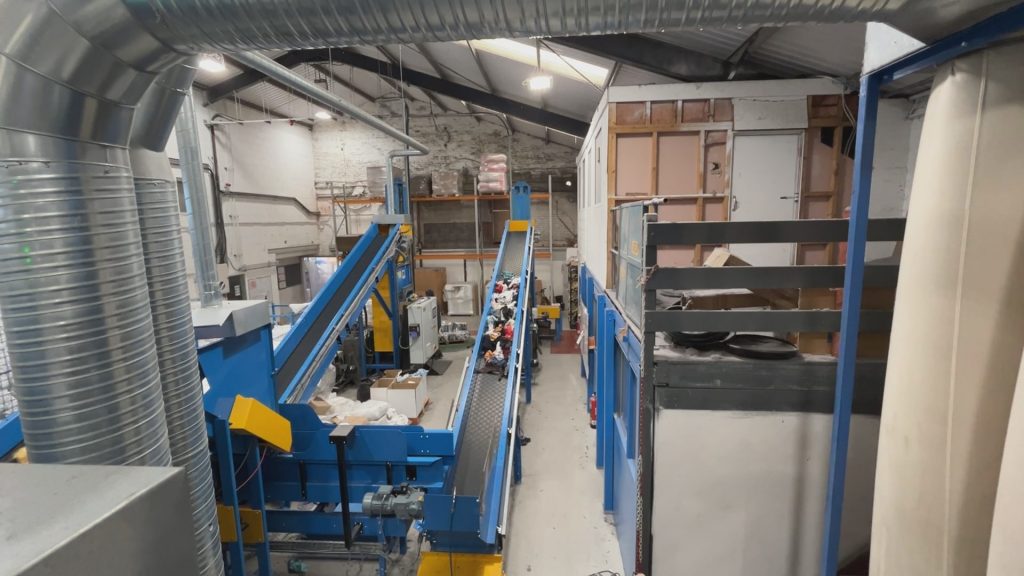
With the dual K10 baler configuration, businesses can double their output, as both balers operate simultaneously to maximise efficiency. If one baler requires maintenance, the second continues to process material, reducing downtime and ensuring production continuity. This level of operation not only meets high standards in wiping rag production but also streamlines handling, storage, and shipping, ensuring customers receive a reliable, high-quality product every time.
The K10 balers are built for durability and ease of maintenance, KME’s balers minimise labour costs.
KME’s bale breaker and dual K10 baler system offers a robust solution for wiping rag manufacturers focused on scalability, quality, and efficiency. This comprehensive setup supports high-demand production while delivering on the promises of consistency, cost-efficiency, and sustainability.
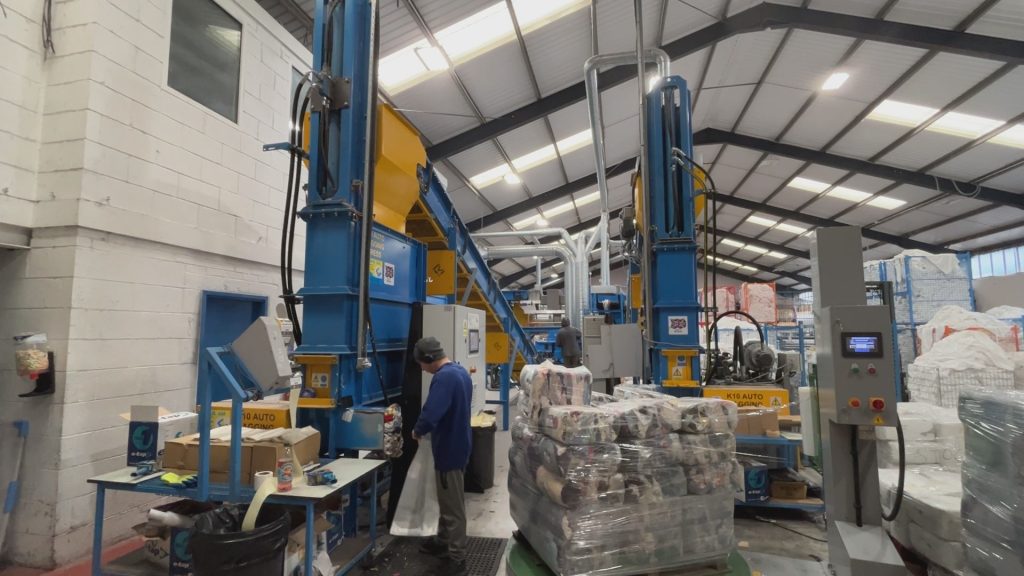
Installing a Ken Mills Engineering (KME) textile bale breaker integrated with two K10 balers can provide significant advantages for businesses focused on wiping rag production. Here are the primary customer benefits:
1. Enhanced Efficiency and Throughput
- Automated Bale Breaking: The KME bale breaker automatically breaks down large textile bales, reducing the need for manual labour and speeding up production.
- Dual K10 Balers: With two balers, the system can handle high volumes of material, allowing for continuous processing without downtime. This means faster overall production rates for wiping rags.
2. Consistent wiping rag Output Quality
- Uniform Bale Feeding: The bale breaker provides a steady, consistent flow of material to the balers, ensuring even density for each bale.
- Minimized Material Variability: By breaking down bales uniformly, the system reduces inconsistencies in material size and shape, producing a more consistent quality for wiping rags.
3. Reduced Labor Costs
- Automated Operations: Automation reduces the need for manual labour in handling and feeding bales, which can lead to significant savings in labour costs.
- Simplified Maintenance: Ken Mills Engineering designs its machinery for ease of use and maintenance, minimising labour required for routine operations.
4. Improved Safety for wiping rag production
- Reduced Manual Handling: By automating bale breaking and compressing, the system minimises heavy lifting, reducing the risk of workplace injuries.
- Enclosed System Design: KME machinery is designed with safety guards and automated controls, which can improve overall workplace safety.
5. Enhanced Productivity and Flexibility
- Quick Processing for Multiple Textiles: The bale breaker and balers are adaptable to different textile types and weights, allowing for efficient processing of various materials.
- Flexible Capacity Management: The dual K10 balers can be used concurrently or independently, enabling the plant to adjust production based on demand, improving responsiveness and productivity.
6. Scalable Investment for Future Growth
- Scalability: This setup can be expanded with additional balers or enhanced automation, making it a scalable investment for growing businesses.
- Long-Term Durability: KME is known for robust, long-lasting machinery, providing value over the years with minimal need for replacement.
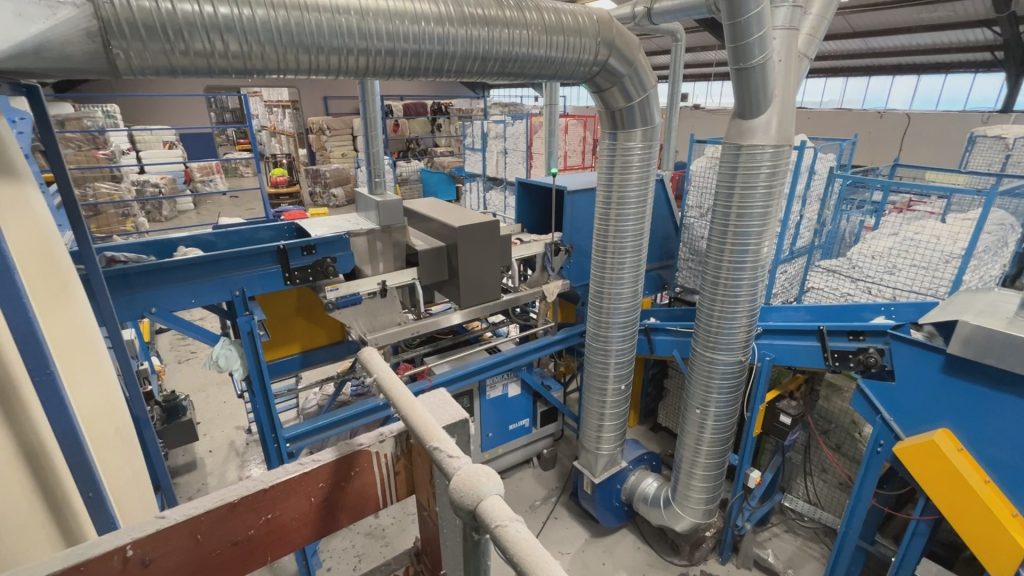