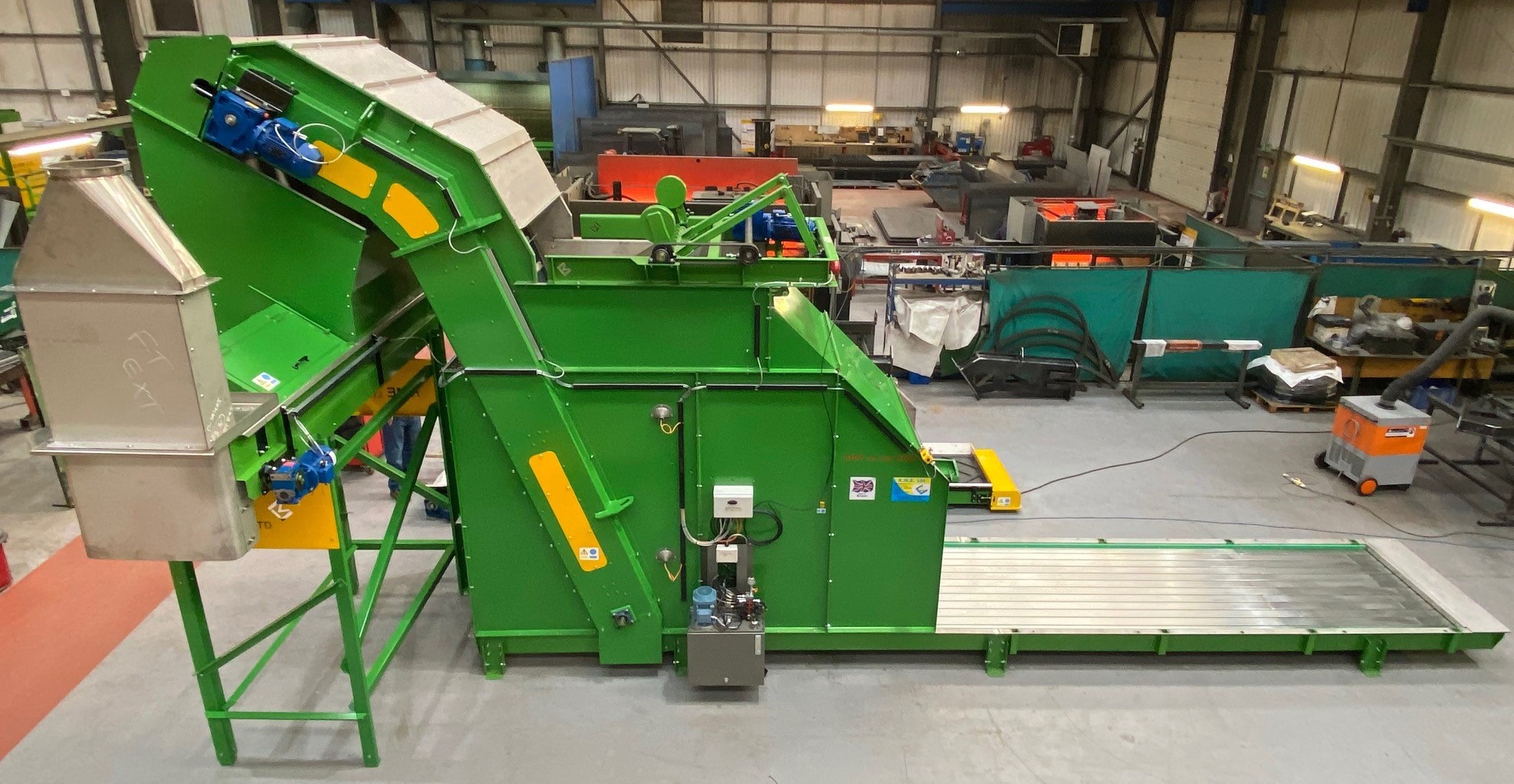
3rd Bale Breaker for US customer
22 Feb 2021
Last week saw the completion of our 3rd bale breaker for breaking hay/haylage/straw for a customer based in America. They are producers and retailers of pet hay and bedding products for animals such as rabbits, guineapigs, rats etc. KME Ltd have been producing quality machinery for over 20 years, for the rebaling of hay for large and small domesticated animals.
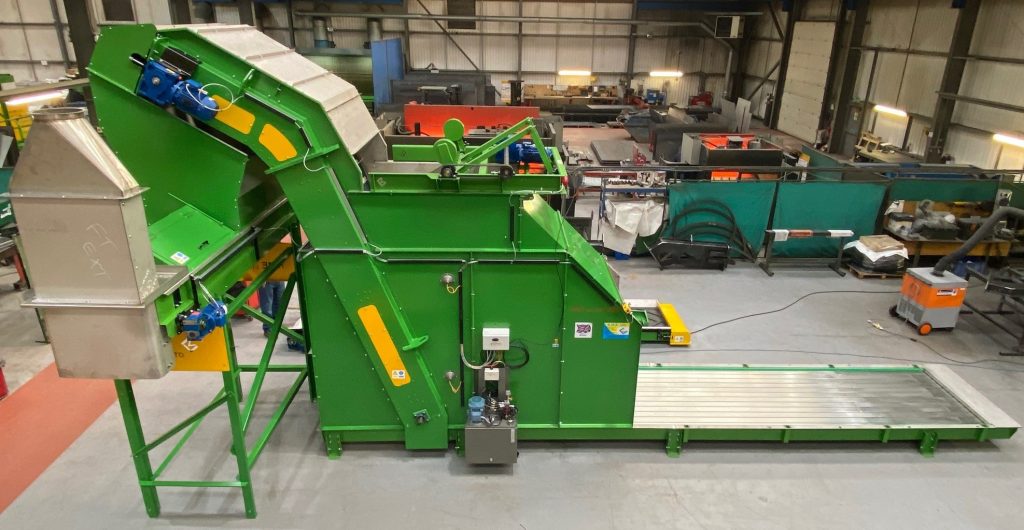
KME first installed a twin line hay breaking system, complete with dust extraction for them back in 2017. Their production rates have since increased and that has called for a 3rd bale breaker to be added.
The new bale breaking line is custom made specifically for the customers needs. All contact surfaces have been fully lined with stainless steel, this allows the end product to be of the highest hygiene quality.

Why Stainless Steel?
It is common for stainless steel to be selected in industry applications, mainly for its resistance to corrosion. However, this is not the only reason for selecting stainless steel. Other criteria such as its aesthetic appearance, its inert, easily cleaned and sterilised.
- durability,
- ease of fabrication
- inert surfaces that can be easily cleaned and offer high levels of hygiene
- Stainless steel remains one of the most hygienic industrial materials known
- easy clean and self-healing surfaces
Dust Extraction – How it works
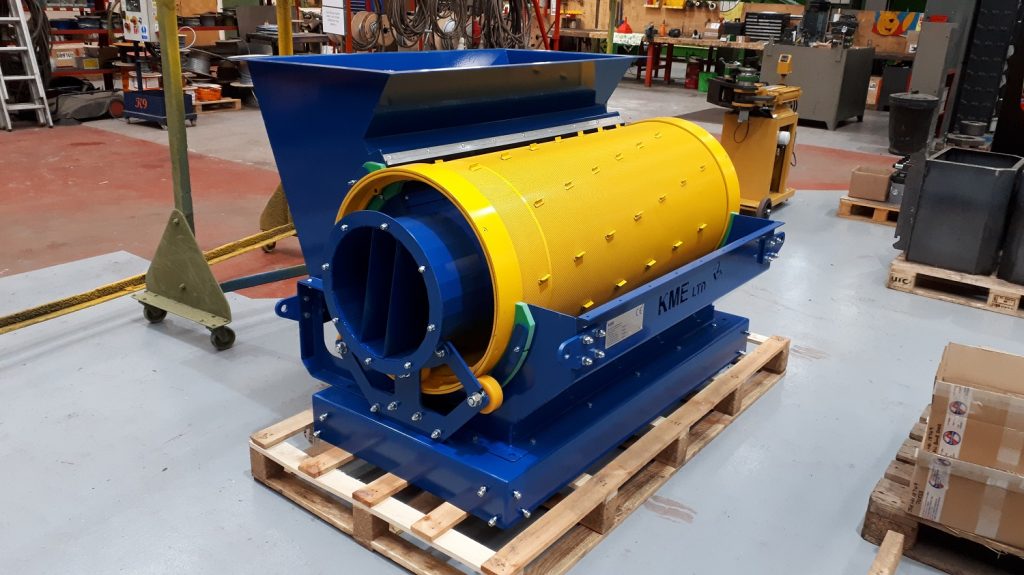
Initially there would be a pick up point at the end of a transfer conveyor coming from the Bale Breaking unit. This would allow for any heavy items to drop from this point, assisting in cleaning up the material. Typically heavy items would include stones, soil etc.
The material from this pick up point would be pneumatically conveyed up into the delivery drum separator. The drum then pulls through the finer / dust type material through a perforated drum into the filter unit. The clean material would fall from the delivery drum ready for further processing.
The air and the dust would continue though the delivery drum and through the fan unit generating the suction.
The air and the dust is fed into a dust filter removal unit where the air is filtered removing the dust and mould spores (>95%). The dust is then collected directly into a plastic bag for disposal or re-purposing. KME can offer varying degrees of filter unit from very basic manually emptied units to automatic emptying systems with rotary valve etc.
Get in touch with us if you have a specific project you need designing.